Traditional textile printing techniques achieved for family business meet digital printing
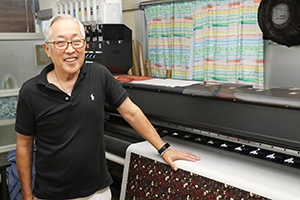
Noriaki Kato, Representative
Conclusive fact in introducing Tx300P-1800
- Challenges for digital textile printing
- Trust in the support system
Grown up as a craftsperson of textile printing long taken over in Yokohama
Have you heard about "Yokohama Nassen (textile printing)" that has over 120 years of history? The textile printing techniques blossomed after the ports of Yokohama opened to foreign trade in 1859, and were developed greatly along with the environment of Yokohama having the wealth of water. It has been passed down until now as a culture of "dyeing" which Yokohama is proud of.
It was in 1948 that my father founded "Kiyoshi Nassen Kojo" in Minami ward, Yokohama. Grown up as the second son of 3 brothers, I moved into the family business naturally. All the 3 brothers placed themselves in the world of Nassen printing after all. While I was acquiring techniques of Nassen as a craftsperson, the company introduced automatic textile printing machines and expanded the business by producing and exporting saris, the national costume of India.
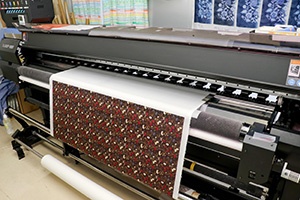
Tx300P-1800
I went independent 10 years ago. It has been 6 years since I started to work with MIMAKI. My experience with MIMAKI started when I bought a Tx-1600 at second hand from an acquaintance.
Later I shifted to Tx2-1600, and now my main operating machine is Tx300P-1800. When we first introduced MIMAKI, we had many troubles, partly due to the difference in the method of use, but the service staff responded to them in good faith, which increased reliability. I have always wanted to utilize our long-cultivated knowledge and techniques of Nassen to meet customers' needs with more free-minded imagination. Meeting MIMAKI may have been inevitable for me with that vision.
Going beyond what Tx300P-1800 can do
Tx300P-1800 is an inkjet printer that emits inks directly onto the textile while feeding it. Inks can be selected to suit the application. Currently, we use reactive dyes for cotton, hemp, silk, etc. that are most demanding for us.
Furthermore, we use the reactive dyes to print even on wools that can originally be printed only with acid dyes. Since wools are animal-based materials, they are embrittled (i.e., fibers are resolved and damaged) if dyed with alkaline reactive dyes. That is where the "Nassen" knowledge and techniques can be used to work out. In digital Nassen, we perform pre-processing by applying adhesive to all over the textile before print. Changing the type and compounding of the adhesive made it possible to print on wools as well without problems. Nassen originally is a technique to dye textiles using colored adhesive which is a mixture of adhesive and dye. Having repeated trials and errors based on such knowledge, we finally found the best compounding condition.
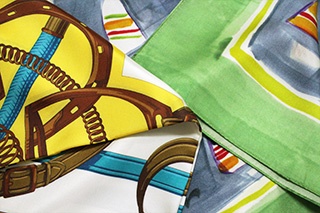
Print on silk
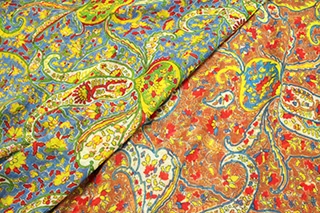
Print on wool
We also succeeded in printing on thin cottons. They are so thin that the ink does not only bleed through, but even passes through backward. After failure upon failure in exploration, we succeeded in raising the quality to the satisfying level. We are happy to see our customers satisfied.
I guess I am truly a craftsperson. I cannot help but keep on wondering how I can do more than what Tx300P-1800 can do. It is a lot of fun and exciting. And if the knowledge I get that way is of help to MIMAKI, that makes me happy.
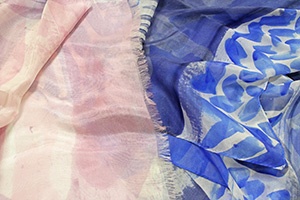
Print on thin textile is also possible.
Issues of multiple processes confronting digital Nassen
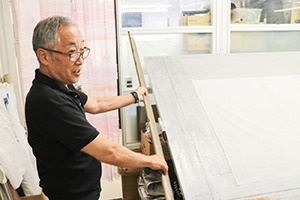
Pre-processing work scenes still remain analog.
In addition to pre-processing before print, digital Nassen also requires post-processing performed after print.
The printed cloths are inspected, then sent to a steaming factory to fix the dye to the fiber, and steamed at high temperature to achieve beautiful coloring. After that, the cloths are sent to a washing factory for water washing process, where they are washed at high temperature to remove the extra adhesives and create a distinctive texture. Then the cloth width is fine-tuned and they are finished to be finally completed as products.
We send cloths to a factory in Yokohama for "steaming", and to a factory in Yamagata for "water washing". But recent freight fare increases are making the situation severe. There used to be lots of steaming and washing factories in Yokohama in the past. It's sad that they have decreased over years. Such situations may be causing young people to find it difficult to enter the world of digital Nassen.
MIMAKI's technology expected to further develop digital Nassen
Conversely, if it becomes possible to perform the "steaming" and "washing" processes in-house instead of outsourcing them, that will be a great news for all of us who are involved in digital Nassen. It will not only reduce the cost, but also realize even shorter production time, and enable us to respond to orders of sample print and small-lot production more effectively than ever.
I recently heard from a sales person that MIMAKI is trying to develop such processes. That is tremendous. We really hope it will come true.
There are small jobs that cannot be handled at large-scale factories, and that is where future creators seek their big dreams. In order to support them, I would like to acquire more new knowledge and technologies as a craftsperson myself. I hope MIMAKI will also keep on making efforts for new challenges.
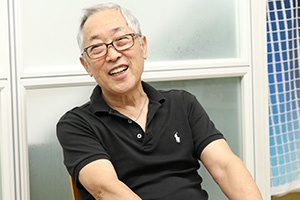
Kiyoshi Print
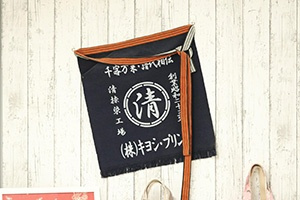
My father, Kiyoshi Kato, founded "Kiyoshi Nassen Kojo" in Yokohama in 1948. Three brothers succeeded the father's business, and strove to acquire the skills as craftspersons of Yokohama’s traditional "Nassen stencil dyeing". After establishing my own business, I have broken new ground in on-demand print, responding to needs of small-lot production of diversified products by utilizing the Nassen techniques. We recently plan and sell our own brand products.
<Introduced products>
Direct-to-Textile Inkjet Printer : Tx300P-1800
Direct-to-Textile Inkjet Printer : Tx2-1600
User profile
- NameKiyoshi Print
- IndustryInkjet print, silk-screen print, tie-dyeing, plain dyeing, etc.
Sale of original brand products - Address2F, 3rd Oba Building, 4-11-8, Chojamachi, Naka-ku, Yokohama-shi, Kanagawa, Japan
- Phone number+81-45-250-0818
- URLhttp://www.kiyoshi-print.jp/