Belt-Type Inkjet Printer High Speed Range Model
Tiger-1800B MkII
Nagano, Japan, May 15, 2018
Mimaki Engineering Co., Ltd. (Mimaki), Headquartered in Nagano Prefecture, Tomi City; President Kazuaki IKEDA announced today the Tiger-1800B MkII to be launched in July 2018, as the successor to the company's previous Belt-Type Inkjet High-Speed range Model, the Tiger-1800B released in September 2016.
The Tiger-1800B MkII is a high speed-range model in pursuit of the print speed and high quality, based on the enhanced stability and high accuracy of print technology.
Covering a broad range of applications, two models are available:
1. Direct print model with 16 print heads (2 lines of 8 print heads in a staggered layout).
2. Transfer sublimation model with 8 print heads (2 lines of 4 print heads in a staggered layout).
With the achievement of a maximum print speed of 385 sqm/h *1 for both models, the Tiger-1800B MkII can cover a wide production range from sample making to small/medium volume printing. An additional new print mode by 1200 dpi is enhancing print quality and the MAPS *2 is an added function for a high quality as well as high-speed printing.
In general, the boundaries of multiple passes to be a line can cause of banding and color shifting when there is just a small gap while printing. MAPS will disperse the edge of each pass to make boundaries look like gradations, eliminating banding and color shifting. To maintain high productivity, another function, the NRS (=Nozzle Recovery System *3), allows printing to continue using good nozzles as substitutes, when clogged nozzles cannot be recovered.
The Tiger-1800B MkII offers outstanding design technology to enhance and maintain stable high-speed printing. Ideal production system can be arranged with enhanced feeding and winding units (for storage after printing) depending on the details of the work and the customers installation environment.
*1: 385 sqm/h: Printed by High speed (3drop) mode 600x600dpi 1 pass 1 Layer Fabric width:1,500 mm
*2: MAPS: Mimaki Advanced Pass System (Described below)
*3: NRS: Nozzle Recovery System (Described below)
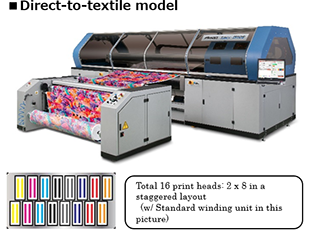
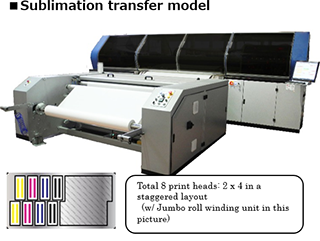
Features
1. Selectable print mode to suit the production
For the realization of higher quality of print, 1,200 dpi print mode is added and the multi-pass is applied.
Printing by single pass may cause a subtle difference of dot diameter or a gap of droplet landing position as it is to be printed by one time for a specified printing area.
The caused gap will appear as stripe and band to be quality degradation.
However, the multi-pass means to print a determined printing area by multiple times with different nozzles, which allows to suppress the cause of stripe and band and create a beautiful print.
The Tiger-1800B MkII will apply the production from the high-speed print regarding much importance for productivity to the high-quality print of beautiful image.
Direct-to-textile Print speed (Bi-direction)
Mode | Resolution | Pass | Layer | Print speed |
---|---|---|---|---|
High speed (3drop) | 600×600 dpi | 1 | 1 | 385m2/h |
Standard (4drop) | 600×600 dpi | 1 | 1 | 295m2/h |
High speed (3drop) | 600×1,200 dpi | 2 | 1 | 210m2/h |
Standard (4drop) | 600×1,200 dpi | 2 | 1 | 155m2/h |
High speed (3drop) | 1,200×1,200 dpi | 2 | 1 | 120m2/h |
Standard (4drop) | 1,200×1,200 dpi | 2 | 1 | 85m2/h |
Transfer sublimation Print speed (Bi-direction)
Mode | Resolution | Pass | Layer | Print speed |
---|---|---|---|---|
High speed (3drop) | 600×600 dpi | 1 | 1 | 385m2/h |
Standard (4drop) | 600×600 dpi | 1 | 1 | 295m2/h |
High speed (3drop) | 600×1,200 dpi | 2 | 1 | 210m2/h |
Standard (4drop) | 600×1,200 dpi | 2 | 1 | 155m2/h |
High speed (3drop) | 1,200×1,200 dpi | 2 | 1 | 120m2/h |
Standard (4drop) | 1,200×1,200 dpi | 2 | 1 | 85m2/h |
2. MAPS:Reliability and stability for the support of high speed print
In general, the boundary of pass to be a line is more likely to become the cause of bandings or color shading by just a small gap while printing.
The MAPS (Mimaki Advanced Pass System) can realize the beautiful printing with less banding and color-shifting by spreading the edge of pass and making the boundary as gradation. *4
*4: MAPS is not available for 1Pass print mode.
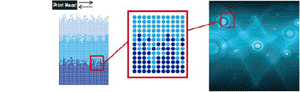
MAPS ON
Beautiful print quality with less banding and color-shifting by spreading the boundary of pass
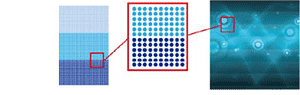
MAPS OFF
Banding is found at the boundary of pass. Stripes and color-shifting are degrading the image quality significantly.
3.NRS *5 : Consecutive operating solution to maintains the productivity
Nozzle problem which is not solved even if cleaning causes the production stop due to machine's downtime till the completing of repair by service staff. NRS (Nozzle Recovery System) is mounted as when a problem occurs in some nozzles, other nozzles will take place to continue to print. Without the operation stop to wait the arrival of service staff, the productivity can be maintained.
*5: NRS is to be applied later. Depending on a print mode, the NRS may not be available.
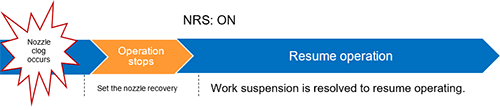
4. Enhanced selectable options according to applications
Extensive lineup of optional devices to be selected according to the type and status of fabric and transfer paper, including the storage after printing.
Optimal introduction is available to suit the production process of customers.
1) Feeding option
(a) Roll media centering unit
Feeding unit for roll media equipped with centering device and tension bar
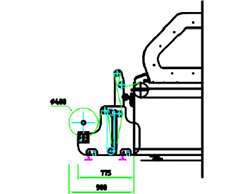
(b) Jumbo roll unit (For direct-to-textile model)
Jumbo roll unit for setting a long length roll fabric
Available to use feeding and winding both
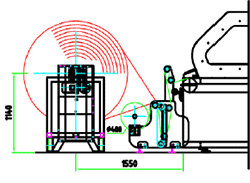
(c) Jumbo roll unit (For transfer sublimation model)
Jumbo roll feeding unit for setting a long length transfer paper
Available Max. diameter to set: 1,000 mm
Available Max. weight to set: 1,000 kg
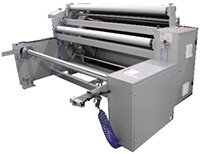
2) Drying/winding option
(a) Large heater unit + Large pleating feeder unit (For Direct-to-textile model)
- Large heater unit
Large heater device
Drying system by electric heater
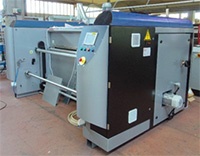
- Large pleating feeder unit
Pleating feeder unit without winding the fabric after dry
Feeding the printed fabric after drying while pleating into receiving box
*Available to set to large heater only
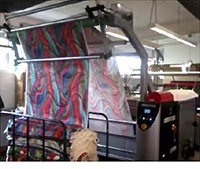
(b) Jumbo roll unit (For Sublimation transfer)
Jumbo roll drying/winding unit for setting a long length sublimation transfer paper
Available Max. diameter to wind: 500 mm
Available Max. diameter to load: 500 kg
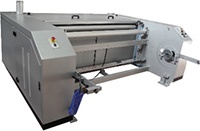
Specifications
Item | Tiger-1800B MkII Direct-to-textile model |
Tiger-1800B MkII Sublimation model |
|
---|---|---|---|
Print head | 16 printheads (8x2 lines in a staggered layout) |
8 printheads (4x2 lines in a staggered layout) |
|
Print resolution | 600 / 1,200dpi | ||
Print speed (Fabric width: 1,500 mm) |
Max. 385 sqm/h *6 | ||
Max. print width | 1,850 mm / 72.8" | ||
Max. media width | 1,900 mm / 74.8" | ||
Ink | Type | Reactive: MLRc500 (Acid/Sublimation/Pigment: To be applied later) |
Sublimation: MLSb510 |
Capacity | 10 kg (ink tank) | ||
Ink set | Reactive: C,M,Y,K,Or,Bl,R,Lk (Acid/sublimation/Pigment: TBD) |
C,M,Y,K | |
Loadable ink color | 8 | 4 | |
Media core diameter | 2 inch *7 | 3 inch *8 | |
Roll weight | 100 kg / 221 lb or less *7 | Feeding: 1,000 kg / 2,205 lb or less *8 Winding: 500 kg / 1,103 lb or less *8 |
|
Roll diameter | 400 mm / 15.7" or less *7 | Feeding: 1000 mm / 39.4" or less *8 Winding: 500 mm / 19.7" or less *8 |
|
Interface | USB 2.0 / Ethernet | ||
Power | Unit: 3-phase 380V ±10%, 65A or less Heater: 3-phase 380V ±10% 40A or less |
||
Operational environment | Temperature: 20 - 25 degC / 68 - 77 degF Humidity: 35 - 65% Rh |
||
Outer dimension (W×D×H) |
Main unit: 5,250 x 2,010 x 2,024 mm (206.7 x 79.1 x 79.7") Feeding unit: 2,240 x 475 x 1,167 mm *7 (88.2 x 18.7 x 45.9") *7 Heater/Winding unit: 2,825 x 1,300 x 1,034 mm *7 (111.2 x 51.2 x 40.7") *7 |
Main unit: 5,250 x 2,010 x 2,024 mm (206.7 x 79.1 x 79.7") Feeding unit: 2,730 x 1,703 x 1,315 mm *8 (107.5 x 67.0 x 51.8") *8 Heater/Winding unit: 2,895 x 2,400 x 1,084 mm *8 (114.0 x 94.5 x 42.7") *8 |
|
重量 | Main unit: 4,750 kg / 1,0472 lb Feeding unit: 130 kg / 287 lb *7 Heater/Winding unit: 840 kg / 1,852 lb *7 |
Main unit: 4,750 kg / 1,0472 lb Feeding unit: 722 kg / 1,592 lb *8 Heater/Winding unit: 1,580 kg / 3,484 lb *8 |
*6: 385m2/h: Printed by High speed (3drop) mode 600×600dpi 1pass 1Layer
*7: It is the value when the standard unit (option) is attached to Feeding/Winding unit of each.
*8: It is the value when the jumbo roll unit (option) is attached to Feeding/Winding unit of each.
* Specifications, designs and dimensions stated in this list may be subject to change without notice due to technical improvement etc.
FESPA Global Print Expo 2018
The Tiger-1800B MkII will be displayed at the Mimaki Stand (#: 1.2- D20-D30) of the FESPA Global Print Expo 2018.
Period: May 15-18, 2018
Venue: Messe Berlin (Berlin Expo Center City, Germany)
Official Website
Contact
MIMAKI ENGINEERING CO., LTD.
Global Marketing Department
1628-1 Shigeno-Otsu, Tomi-city, Nagano 389-0512 JAPAN
Tel: +81-(0)268-80-0078 / Fax: +81-(0)268-80-0041