Pre- and post- processing equipment for digital textile printing
Rimslow Series
Nagano, Japan, May 15, 2018
Mimaki Engineering Co., Ltd. (Mimaki), Headquartered in Nagano Prefecture, Tomi City; President, Kazuaki IKEDA announced today the launch of the "Rimslow Series", their new pre- and post- processing equipment for digital textile printing comprising a new pre-treatment unit, two steamers and one washer newly added to their product lineup in October 2018. These products are from the Australian company Rimslow Global Pty. Ltd., which Mimaki acquired in November 2017.
For textile printing by an inkjet printer, it involves the following four processes;
1. Pre-treatment: Preventing ink bleeding by applying a treatment agent to the fabric.
2. Printing: Printing with an inkjet printer.
3. Steaming: Fixing the printed ink onto the fabric.
4. Washing: Washing off extra ink and treatment agent from the fabric.
The current textile digital printing is requiring purchasing printers and pre- and post- processing devices from different manufacturers.
The production conditions depending on the fabric, ink and production place will be one of the important factors which control the finished quality (print penetration, image quality, color density, and dyeing property) and fixing up those conditions required much cost, time and knowledge.
The workflow of textile printing by inkjet printer

By providing pre-treatment unit, printer, steamer and washer as the completed system from Mimaki, it is possible to offer a total solution including equipment, recommended production conditions and know-how and easier for customers to proceed a new entry into digital printing business and in-house production.
As well, regarding direct sublimation printing, currently purchasing a pre-treated fabric was necessary but using the pre-treatment unit of "Rimslow Series" can realize the in-house work of pre-treatment process.
The unification of all the required equipment into Mimaki products will minimize the down time of machines for saving both time and money, as everything from initial consultation to production troubleshooting can be all handled by Mimaki.
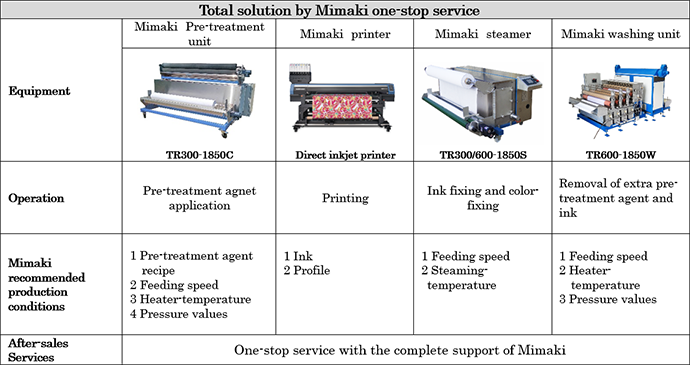
Lineup / Specifications
TR300-1850C Pre-treatment unit
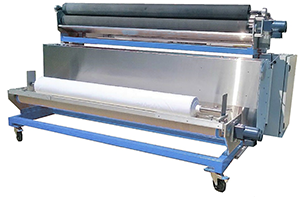
Features
- Applying a pre-treatment agent before printing.
- Applying pre-treatment agent can control the penetration, density and dyeing property.
- Space saving drying heater can be installed at any location.
Item | TR300-1850C |
---|---|
Maximum media width | 1,850 mm [72"] |
Maximum media diameter | 300 mm [11.8"] |
Maximum settable temperature (drying) | 100 degC [212 degF] |
Maximum processing speed | 75 lm (Linear meter)/h |
Tray capacity for agent application | 25 L |
Tank capacity (Pre-treatment agent) | 50 L |
Heater power | Electricity |
Power supply | 3-phase 4-wire AC400V±5%, 50/60Hz±1Hz 32A or less |
Power consumption | 18 kW |
Water consumption | N/A (Only required for cleaning) |
Compressed air | 200 L/min. at 6 bars |
Dimensions (WxDxH) | 2,600 x 1,700 x 1,100 mm [102.4 x 66.9 x 43.3"] |
Weight | 380 kg [838 lb] |
TR300-1850S Steamer
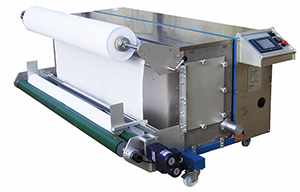
Features
- Steamer for dye fixing onto the printed fabric and coloring the printed ink.
- Compact design allows feeding and winding of the fabric from the front of the machine.
Item | TR300-1850S |
---|---|
Maximum media width | 1,850 mm [72"] |
Maximum media diameter | 300 mm [11.8"] |
Maximum settable temperature (steaming) | Saturated steam: 102 degC [215.6 degF] Overheat steam: 180 degC [356 dgF] |
Maximum processing speed | 55 lm (Linear meter)/h |
Fabric length | 6 m |
Tank capacity (Water) | 25 L |
Heater power | Electricity |
Power supply | 3-phase 4-wire AC400V±5%, 50/60Hz±1Hz 32A or less |
Power consumption | 12 kW |
Dimensions (WxDxH) | 2,500 x 1,600 x 1,300 mm [98.4 x 63.0 x 51.2"] |
Weight | 480 kg [1,058 lb] |
*Water supply is required for the inner tank (25 L) from the water supply port by hose or plastic tank.
TR600-1850S Steamer
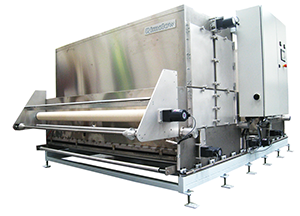
Features
- Steamer for dye fixing onto the printed fabric and coloring the printed ink.
- High productivity contributes to high-speed printing of 260 lm/h.
Item | TR600-1850S |
---|---|
Maximum media width | 1,850 mm [72"] |
Maximum media diameter | 300 mm [11.8"] |
Maximum settable temperature (steaming) | Saturated steam: 102 degC [215.6 degF] Overheat steam: 180 degC [356 dgF] |
Maximum processing speed | 260 lm (Linear meter)/h |
Fabric length | 26 m |
Tank capacity (Water) | 50 L |
Heater power | Electricity |
Power supply | 3-phase 4-wire AC400V±5%, 50/60Hz±1Hz (Amp:TBD) or less |
Power consumption | 18 kW |
Dimensions(WxDxH) | 2,600 x 2,900 x 1,600 mm [102.4 x 114.2 x 63.0"] |
Weight | 1,640 kg [3,616 lb] |
TR600-1850W Washer
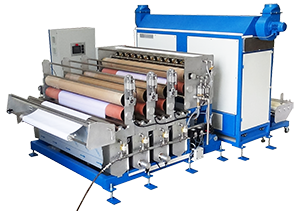
Features
- Washer for eliminating leftover pre-treatment agent and ink after steaming.
- Hybrid model that can be used as pre-treatment device, as well.
- Equipped with four washing tanks and a spray washing system.
Item | TR600-1850W |
---|---|
Maximum media width | 1,850 mm [72"] |
Maximum media diameter | 300 mm [11.8"] |
Maximum settable temperature (drying) | 180 degC [356 dgF] |
Maximum processing speed | 130 lm (Linear meter)/h |
Tray capacity for agent | 24 L |
Tank capacity (Washing) | 340 L x 4 |
Heater power | Electricity |
Power supply | 3-phase 4-wire AC400V±5%, 50/60Hz±1Hz 100A or less |
Power consumption | 66 kW |
Water consumption | 600 L/h |
Compressed air | 1,500 L/min. at 6 bars |
Dimensions (WxDxH) | 2,700 x 4,200 x 2,400 mm [107 x 166 x 95"] |
Weight | Washing unit = 1,420 kg [3,131 lb] Electrical box = 60 kg [132 lb] Drying unit = 800 kg [1,764 lb] Winder = 150 kg [331 lb] |
*Commercial plastic tank of 50 L capacity is required for pre-treatment.
* Specifications, designs and dimensions stated in this list may be subject to change without notice due to technical improvement etc.
Mimaki IoT for the TA Market
A software "Mimaki Job Controller™ TA" will be also announced for the realization of three functions, "Production condition management", "Production condition reading by barcode scanning" and "Visualization of production data-base" using the network connection of Rimslow products and printers.
The total solution system including "Rimslow Series" and the "Mimaki Job Controller™ TA" will be displayed at the Mimaki Stand (#: 1.2- D20-D30) of the FESPA Global Print Expo 2018.
FESPA Global Print Expo 2018
Period: May 15-18, 2018
Venue: Messe Berlin (Berlin Expo Center City), Berlin, Germany
Official Website
Contact
MIMAKI ENGINEERING CO., LTD.
Global Marketing Department
1628-1 Shigeno-Otsu, Tomi-city, Nagano 389-0512 JAPAN
Tel: +81-(0)268-80-0078 / Fax: +81-(0)268-80-0041