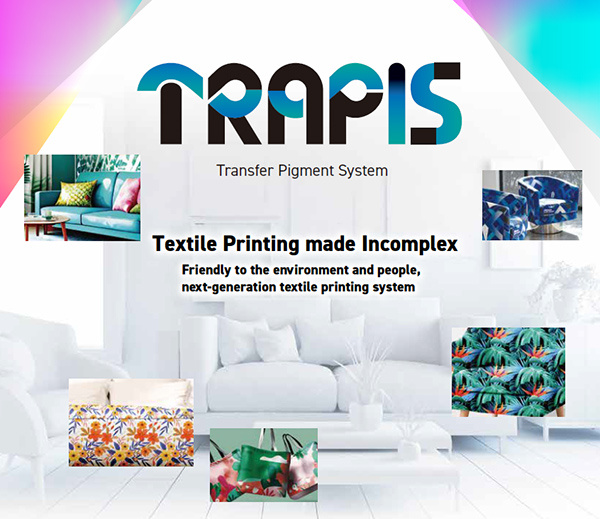
Nagano, Japan, March 13, 2024
Mimaki Engineering Co., Ltd. (Head office: Tomi-shi, Nagano, Pref.; President: Kazuaki Ikeda), specializing in industrial inkjet printers, cutting plotters and 3D printers, is pleased to announce the launch of “TRAPIS”, environmentally and people-friendly next-generation textile printing system, which is a commercialized version of the “textile pigment transfer printing system” that was exhibited at ITMA in June 2023. Prior to its product launch, it will be exhibited for the first time in the world at the FESPA Global Print Expo 2024 to be held in March 2024 (venue : Amsterdam, the Netherlands) where it will propose “Textile Printing made Incomplex” that can cut wastewater amount by about 90% (compare to conventional method), “easily operated by anyone” and “Installable in any locations”.
“TRAPIS” is the company’s pigment transfer textile printing system, whose name is derived from the words “Transfer”, “Pigment”, and “System”. The system consists of ur inkjet printer, dedicated ink, dedicated transfer paper, and a dedicated transfer machine made by a European manufacturer recommended by us. (Figure.1)
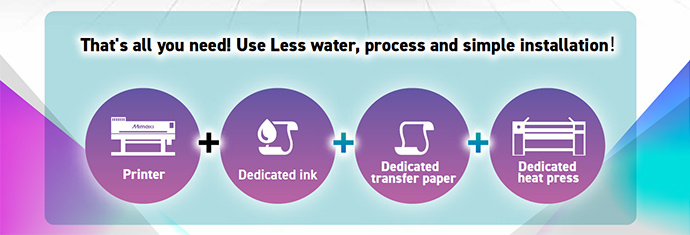
Fig.1 TRAPIS System configuration
The conventional textile dyeing method (Figure.2) generates a large amount of wastewater mixed with chemical substance (about 14.5 liters per square meter in the case of digital dye printing*1) due to pre- and post-treatment of textile, which is considered an environmental problem, In addition, the dyeing process is complex, requiring specialized skills and knowledge, and the investment of dyeing equipment requires large-scale wastewater treatment facilities, limiting the location where they can be installed.
*1 Digital dye printing generates significant amount of wastewater by textile printing conveyor belt washing and fabric washing after dye fixation (steam) (by our original research)
In the TRAPIS, a design printed on a special paper is transferred to the fabric using a heat transfer machine to complete the textile printing process. Therefore, the process generates almost zero wastewater (only water in the waste ink generated by printer’s automatic maintenance), and even including wastewater generated in the transfer paper manufacturing process, wastewater is cut by approx. 90% compared to conventional digital dyeing systems. Since the system does not require a large space or wastewater treatment facilities like conventional system, it can be installed in a small space, and textile printing business can be conducted at the forefront of fabric supply distribution (store, design offices, etc.) (Figure.3)
In addition, since the process is simple that is completed by printing and transferring, and does not require specialized dyeing expertise and knowledge, anyone can easily initiate the operation.
Furthermore, in conventional textile printing, it is necessary to use different dyes (ink types) by types of textiles. TRAPIS, however, can print on a wide range of textile with one type of ink (Figure.4). Therefore, it is not limited to dyeing factories that specialize in textile printing, but enables dyeing business to operate in any locations, on a multi-variety of textile, in a short-run as required, thus adapting the global dyeing industry’s demand for sustainability.
TRAPIS will be compatible with the printing of each textile materials and is scheduled to go on sale in June 2024. We expect to sell 100 units per year (worldwide) in the textile and apparel market, including fashion apparel and home textile applications.
Mimaki Engineering Co., Ltd. with its management vision of “Something New, Something Different,” will continue to pursue new technological innovations to achieve the “beauty and speed” that our customers demand.
Features of TRAPIS
- Simple textile printing system that requires only printing and transferring, so it can be easily operated by anyone without the need for specialized skills or knowledge as with conventional textile printing system.
- Installable in small space, and textile printing business can be conducted at the forefront of fabric supply distribution (store, design offices, etc.)
- The process generates almost zero wastewater. And even including wastewater generated in the transfer paper manufacturing process, wastewater is cut by approx. 90% compared to conventional digital dyeing systems.
- Printing on multi-variety textile fabrics with a single type of ink
- Printing on transfer paper eliminates the need for complicated maintenance of fabric conveyor belt, as is the case with conventional digital textile printing.
- Colours are as good as those of conventional textile dyeing, and light fastness of printed fabrics to be up to the standard level.
- Ink is certified ZDHC MRSL Lv.3*2. Worker and consumer safety and environmentally friendly products.
*2 ZDHC is a non-profit organization based in Amsterdam, the Netherlands, that works to eliminate the emission of hazardous substances in the textile and leather industry.
Exhibition overview
Name: FESPA Global Print Expo 2024
Dates: March. 19, 2024[Tue] - March. 22, 2024[Fri]
Place: Amsterdam RAI (Amsterdam, the Netherlands)
Stand #: Hall 12 / Stand F10
About Mimaki Engineering
Mimaki Engineering develops, manufactures, sales, and maintains industrial inkjet printers, cutting plotters, 3D printers, inks, and software. By providing total solutions for the printing process for the sign graphics, industrial products, and textile apparel markets, we aim to be an innovator that constantly delivers "Something New, Something Different" to our customers.
Company/IR website: https://ir-eng.mimaki.com/
Product website: https://mimaki.com/
Contact
MIMAKI ENGINEERING CO., LTD.
Global Marketing Department
1628-1 Shigeno-Otsu, Tomi-city, Nagano 389-0512 JAPAN
Tel: +81-(0)268-80-0078 / Fax: +81-(0)268-80-0041