Belt-Type Direct-to-Textile Inkjet Printer High-Speed Range Model
Pro series
Tiger-1800B / Leopard-1800B / Fox-1800B
Nagano, Japan (August 24, 2016)
Mimaki Engineering Co. Ltd. (President and Representative Director: Kazuaki Ikeda), a leading global manufacturer of wide format inkjet printers and cutting plotters, announces that it will launch Pro series (including Tiger-1800B, Leopard-1800B, and Fox-1800B), a line of belt-type direct-to-textile inkjet printers. The Pro series are developed by Italy’s La Meccanica S.p.A. and will be available in September, 2016.
La Meccanica S.p.A, scheduled to become a subsidiary of the Mimaki group through full acquisition, is a leading manufacturer in the development, production, and sales of mostly high-speed, high-end textile inkjet printer models. This will be a welcome expansion of our existing line of medium-speed, entry model textile inkjet printers. Utilizing the know-hows from La Meccanica S.p.A as the foundation of our accelerated high-end model development, this addition will give us a powerful product line-up for the textile and apparel market by delivering large-scale production at manufacturing sites and small-scale production near consumption sites.
The Pro Series, with its outstanding stability and high-precision printing technology, is a high-speed range model dedicated to speed and beautiful printing. The three products offered in this series will complete our line-up by filling the gap between our medium-speed digital textile inkjet printer Tx500-1800B (maximum printing speed: 140 m2/h (*1)) and our high-speed digital textile inkjet printer MM700-1800B (maximum printing speed: 800 m2/h (*2)). With a maximum printing speed of 390 m2/h (*3), Tiger-1800B fits high-volume productions that were printed by analog printing methods. Leopard-1800B can be used in a wide range of applications from sample creation to small lot production. Fox-1800B, with four heads, is an even more compact and economical model than Leopard-1800B.
The Pro series provides a reliable operation supported by excellent technical capabilities. Twin pressure roller shafts and a wrinkle/jam sensor secures a stable textile transportation. A degassing module maintains stable ink-jetting. Furthermore, various optional units, including feeding/take-up units are offered to fit diverse production needs and factory environments.
*1: Draft mode (300 × 300 dpi, 2pass)
*2: Draft mode (300 × 300 dpi, 2pass)
*3: High-definition mode (600 × 600 dpi, 1pass) Textile width: 1,500 mm
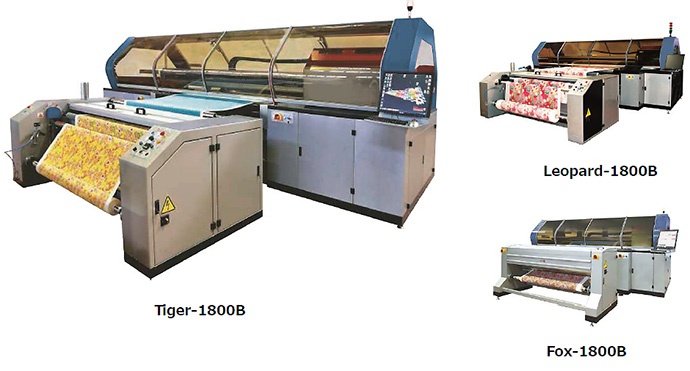
Product outline
- Each of three models delivers exceptional print speed
To meet users' production needs, we provide three models. Each model has different print speed, as described below:
Tiger-1800B | Maximum print speed: 390 m2/h (*3) | Standard print speed: 220.5 m2/h (*4) 16 printheads arranged in two staggered lines. Tiger-1800B fits high-volume productions that were printed by analog printing methods. *3: High-definition mode (600 × 600 dpi, 1 pass) Textile width:1,500 mm *4: High-definition mode (600 × 600 dpi, 2 pass) Textile width:1,500 mm |
Leopard-1800B | Maximum print speed: 244.5 m2/h (*5) | Standard print speed: 127.5 m2/h (*6) 8 printheads arranged in-line. Leopard-1800B can be used in a wide range of applications from sample creation to small lot production. *5: High-definition mode (600 × 600dpi, 1 pass) Textile width: 1,500 mm *6: High-definition mode (600 × 600dpi, 2 pass) Textile width: 1,500 mm |
Fox-1800B | Maximum print speed: 240 m2/h (*7) | Standard print speed: 130.5 m2/h (*8) 4 printheads arranged in-line. Fox-1800B, with four heads, is an even more compact and economical model than Leopard-1800B. Suitable applications are small lot production and sample creation. *7: High-definition mode (300 × 300 dpi, 1 pass) Textile width: 1,500 mm *8: High-definition mode (300 × 300 dpi, 2 pass) Textile width: 1,500 mm |
- Stable and reliable mechanism secures high-speed printing
- Textile is uniformly applied onto the transportation belt by twin pressure roller shafts attached to the edge of the belt. Additionally, the wrinkle and jam sensors minimize the damage to the printhead through early detection of wrinkles and jams.
- The degassing module eliminates air bubbles in the ink to prevent missing nozzles and deliver stable ink-jetting.
- Each printhead is automatically cleaned by a dedicated wiper. This function saves the maintenance time and improves the print quality by avoiding color mixing in the printheads. - High-precision droplet control technique delivers beautiful print results
Variable dot printing enables the use of varying droplet sizes depending on the ink type and print mode in order to achieve smooth gradation printing. High-definition mode (*9) uses three different droplet sizes. High-dense mode (*10) uses four different droplet sizes.
*9: The high-definition mode uses droplets among 4, 7, and, 12 picoliters.
*10: The high-dense mode uses 4, 7, 12, and 18 picoliters - Extensive optional units for accommodating various applications
To meet diverse material and production needs, The Pro series provides various optional units:
- Feeding units for jumbo rolls or folded fabrics
- Heating units
- Folding arm unit for storing fabric in the box after printing - Large-sized ink tank (10 kg) ensures cost-effective print operation.
The bulk ink supply enables effective long-hour printing while reducing the operational cost.
Main Features
1. All three models deliver exceptional print speed
To meet a range of production needs, the print speed of each model can be varied by changing the number and configuration of printheads. In addition, two variable droplet print modes are provided: High-definition with three droplet sizes ranging from 4 to 12 pl, high-dense mode with four droplet sizes ranging from 4 to 18 pl. Print speed is different depending on the print mode.
1) Tiger-1800B
Tiger-1800B features 16 printheads arranged in two staggered lines. It achieves maximum print speeds of up to 390 m2/h (*11) in high-speed and 220.5 m2/h (*12) in standard speed.
*11: High-definition mode (600 × 600 dpi, 1 pass) Textile width: 1,500 mm
*12: High-definition mode (600 × 600 dpi, 2 pass) Textile width: 1,500 mm
Configuration of printhead
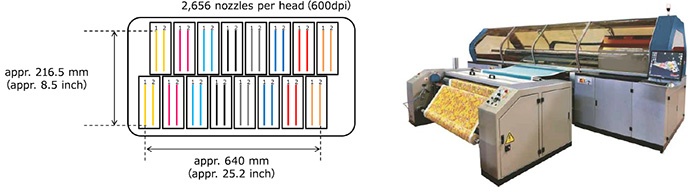
Print speed (Textile width: 1,500 mm)
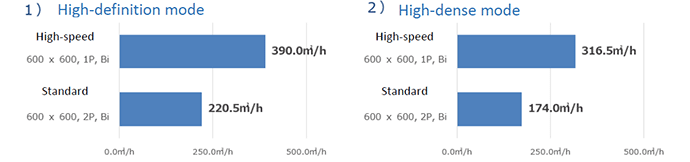
2) Leopard-1800B
Leopard-1800B features eight printheads arranged in an in-line configuration and achieves maximum print speeds of up to 244.5 m2/h(*13) in high-speed and 127.5 m2/h(*14) in standard speed.
*13: High-definition mode (600 × 600 dpi, 1 pass) Textile width: 1,500 mm
*14: High-definition mode (600 × 600 dpi, 2 pass) Textile width: 1,500 mm
Configuration of printhead
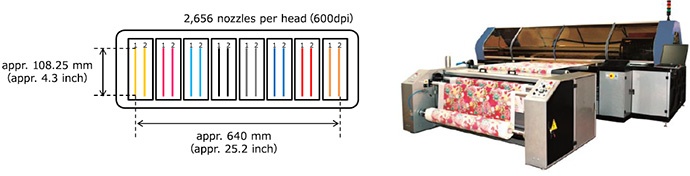
Print speed (Textile width: 1,500 mm)
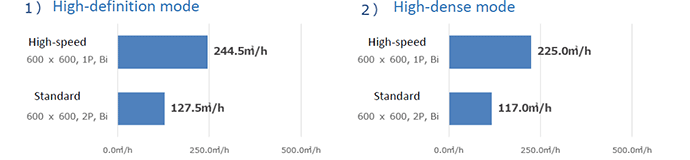
3) Fox-1800B
Fox-1800B features four printheads arranged in an in-line configuration and achieves maximum print speeds of up to 240 m2/h(*15) in high-speed and 130.5 m2/h(*16) in standard speed. Four print speeds are provided: High-speed, Standard 1, Standard 2 and High-quality.
*15: High-definition mode (300 × 300 dpi, 1 pass) Textile width: 1,500 mm
*16: High-definition mode (300 × 300 dpi, 2 pass) Textile width: 1,500 mm
Configuration of printhead
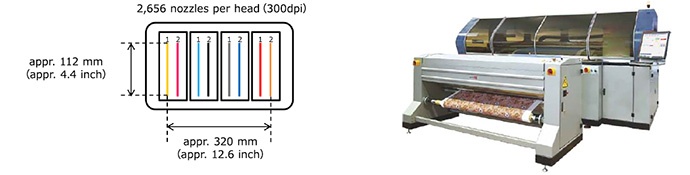
Print speed (Textile width: 1,500 mm)
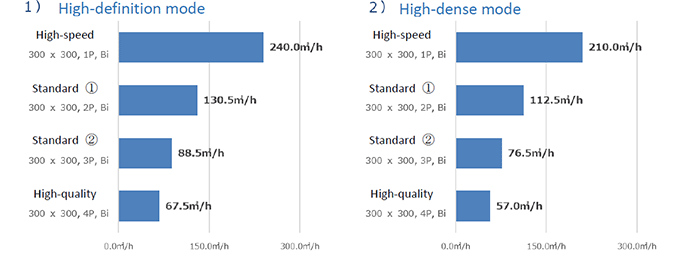
2. Stable and reliable mechanism secures high-speed printing
1) Stable textile transportation mechanism
Textile transport security is achieved by the twin pressure roller shafts attached to the edge of the transportation belt. Textiles are uniformly applied without wrinkling onto the belt through the upper and lower rollers (Fig. 1), assuring stable textile transportation. Furthermore, the wrinkle and jam sensors detect textile wrinkling or creasing early in order to minimize potential damage to the printheads from collisions with raised or jammed textiles.
FIG.1: Textile path diagram
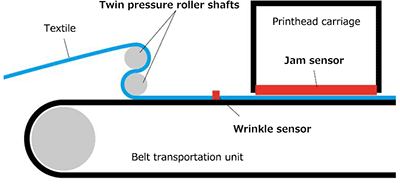
2) Degassing module and ink circulation mechanism maintain optimum ink conditions
Air bubbles generated in the ink can lead to missing nozzles because such bubbles act as cushions that decrease ink ejection power. To assure stable ink-jetting, each model of the Pro series has a degassing module that removes bubbles and constantly circulates ink.
Illustration of Degassing module
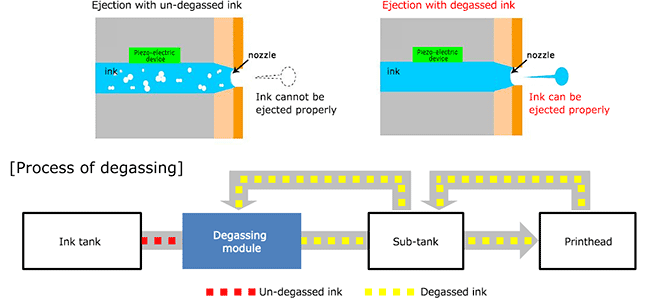
3) Automatic wiper cleaning
Cleaning liquid is automatically applied to each wiper before and after head cleaning. This liquid enhances the cleaning effect during the head-cleaning process, ensuring a clean wiper and reducing daily maintenance time. Furthermore, as each printhead has its own wiper, quick and effective cleaning is enabled while color mixing in the printheads is avoided.
3. High-precision droplet control technique to deliver beautiful print results
“Variable dot printing” delivers less granular, smooth quality printing using different ink droplet sizes depending on ink type or print mode. The Pro series products offer two modes: high-definition mode uses 4, 7, and 12-pl droplets and is suitable for printing fine-design patterns or pale-colored graphics; high-dense mode uses 4, 7, 12, and 18-pl droplets and is suitable for printing patterns that require high ink density.
Illustration of variable dot printing
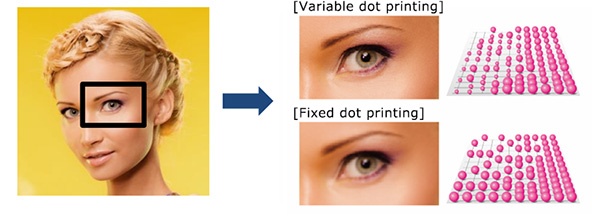
4. Extensive optional units for accommodating various applications
Various optional units are offered to fit a range of production needs
1) Feeding units
Rolled textile feeding unit
This unit is used for feeding rolled textiles and is equipped with a centering system and tension bars
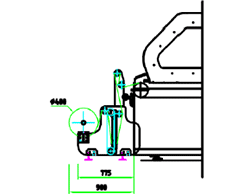
Jumbo roll feeding unit
This unit is used for feeding large-sized, long-rolled media and can be used with the feeding and take-up units.
*This unit cannot be used with Fox-1800B
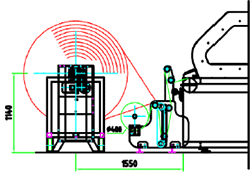
2) Drying and Take-up units
Large heating unit + Folding arm unit for Tiger-1800B
- Large heating unit
This electric heating unit is designed for Tiger-1800B.
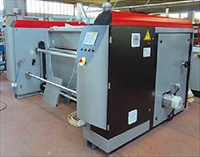
- Folding arm unit
This unit folds and stores printed textiles in a box without interrupting textile transportation.
* This unit can only be connected to the large heating unit
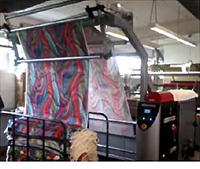
5. Large-sized ink tank (10 kg) ensures cost-effective print operation
The bulk ink supply delivers cost-effective printing and enables long-hour printing. Furthermore, the printer monitors the ink level using a laser sensor and displays an alert on the operation panel when the ink level is low.
Specifications
Tiger-1800B | Leopard-1800B | Fox-1800B | ||
---|---|---|---|---|
Printhead | 16 Staggered arrangement (Each line has 8 printheads) |
8 Single in-line arrangement |
4 Single in-line arrangement |
|
Print resolutions | 600dpi | 600dpi | 300dpi | |
Print speed (Textile width: 1,500 mm) |
High-speed: 390 m2/h (*17) Standard speed: 220.5 m2/h (*18) |
High-speed: 244.5 m2/h (*19) Standard speed: 127.5 m2/h (*20) |
High-speed: 240 m2/h (*21) Standard speed: 130.5 m2/h (*22) |
|
Maximum print width | 1,850mm | |||
Maximum media width | 1,900mm | |||
Ink | Type | Reactive/Acid/Sublimation/Pigment | ||
Packaging | 10 kg (22 lb) tank | |||
Ink set | Reactive: C, M, Y, K, Or, Bl, R, Lk Acid/Sublimation/Pigment: To be determined |
|||
Loadable ink color | 8-color | |||
Roll core diameter | 2 in | |||
Roll outer diameter | 400 mm (15.75 in) | |||
Roll weight | 100 kg (220.5 lb) or less | |||
Interface | USB 2.0 / Ethernet | |||
Power supply | Three -phase 380V ± 10% / Main unit 65 A or less / Heater 40 A or less | |||
Operational environment | Temperature: 20°C–25°C (68°F–77°F) / Humidity 35%–65% Rh | |||
Dimensions (W×D×H) | Main unit: 5,250 mm × 2,350 mm × 2,000 mm (206.7 in × 92.5 in × 78.7 in) Heater: 2,825 mm × 1,300 mm × 980 mm (111.2 in × 51.2 in × 38.6 in) |
Main unit: 4,600 mm × 2,150 mm × 1,800 mm (181.1 in × 84.7 in × 70.9 in) Heater: 2,825 mm × 1,300 mm × 980 mm (111.2 in × 51.2 in × 38.6 in) |
Main unit: 4,200 mm × 2,100 mm × 1,850 mm (165.4 in × 82.7 in × 72.8 in) Heater: 2,565 mm × 800 mm × 1,000 mm (101 in × 31.5 in × 39.4 in) |
|
Weight | Main unit: 5,120 kg (11,290 lb) Heater: 805 kg (1,775 lb) |
Main unit: 3,450 kg (7,606 lb) Heater: 805 kg (1,775 lb) |
Main unit: 2,800 kg (6,173 lb) Heater: 250 kg (551.2 lb) |
Note: For product improvement purpose, data in above specifications are subject to change without notice.
*17: High-definition mode (600 × 600 dpi, 1pass) *18: High-definition mode (600 × 600 dpi, 2pass) *19: High-definition mode (600 × 600 dpi, 1pass) *20: High-definition mode (600 × 600 dpi 2pass) *21: High-definition mode (300 × 300 dpi, 1pass) *22: High-definition mode (300 × 300 dpi, 2pass)
Contact
Mimaki Engineering Co., Ltd.
Sales Division
Postal code: 389-0512
Address: 1628-1 Otsu Shigeno Tomi Nagano, Japan
Tel: +81-(0)268-64-2281, Fax: +81-(0)268-80-0041